Diesel Fuel Filtration
- Ernest Domingue, P.E.
- Jul 15, 2019
- 8 min read
Updated: May 12, 2022

In an earlier article, our focus was centered around the importance of fuel quality monitoring and fuel treatment, while the topic of fuel filtration was only touched upon. This article focuses on diesel fuel filtration and the importance of selecting the right filters for today's rigorous operating conditions.

In order to meet environmental regulations of Tier 4 exhaust emissions standards, diesel engine generator manufacturer’s have increased their fuel system injection pressures upwards of 30,000 PSI. The higher injection pressures result in better atomization of the fuel and effectively reduces emissions. Conversely, these higher pressures increase abrasive wear of the injectors which are cooled by the fuel making it more important than ever before to select filtration equipment that is appropriate for today's requirements. Proper filtration must adequately remove the two worst enemies of diesel engines: water and particulate contaminants.
Water Contaminant
As we pointed out before, it is very important to keep the stored fuel clean and dry. Water in the fuel, either emulsified or suspended as tiny droplets, can damage injectors. The fuel system provides cooling and lubrication for the injectors. Water will break down the film layer of the lubricating fuel oil and cause more metal to metal contact of the close tolerance parts of the engines fuel system.
Particulate Contaminant
Microscopic particles that make it through the primary and secondary filters are abrasive at the extremely high injection operating pressures of the engine fuel system. More emphasis should be placed on selecting filters that efficiently remove microscopic particle sizes to help protect against long term engine wear and damage.

Proper Filtration
Breather Vents
Keeping moisture and particulates out of the stored fuel system should begin at the bulk storage tank. Clean and dry fuel delivery can be controlled by using reputable fuel suppliers that employ proper operating procedures, but the outdoor tank vent is a source of moisture and dust that can be controlled better with the use of adsorption technology. Adsorption is the removal of moisture that is still in the vapor state using a desiccant type filter and thus trapping and preventing this moisture from condensing to water (condensation) inside the fuel storage system. Breather type vents such as the one depicted to the left, when used in place of a conventional rain cap can prevent moisture from condensation and dust from the atmosphere from migrating into the bulk storage tank. The filter cartridge of the breather type vent, a self-regenerating moisture adsorption media, is also highly efficient (about 97%) down to the 3 micron particle size. Regeneration of the desiccant occurs during the natural two way movement of the vented air. When fuel is delivered the air vents outward of the tank and when fuel is used air vents inward to the tank. About all that is required for maintenance is the Manufacturer’s recommended annual replacement of the filter cartridge.
Strainers

Strainers provide a coarse filtration meant to protect the fuel transfer pumps but also benefit the engine by removing particulates ahead of the engine. Fuel transfer pumps are positive displacement using gear or screw type impellers which have close tolerances that should be protected by the use of strainers. At the location of the fuel pump inlet, 40 mesh strainer size is recommended in order to keep pressure drop low and provide safe pump operation within the pump’s suction pressure limits or “vacuum” capability which for most fuel transfer pumps is around 12 to 15 in. Hg. maximum vacuum. It is always good practice to plan for dual strainers in parallel with valving that allows one in use while the other is being serviced and cleaned during operation.
If it is feasible, a second set of strainers using a finer 100 or 200 mesh basket should be used on the discharge side of the transfer pumps prior to the indoor day tanks. Positive displacement fuel transfer pumps can be selected with up to 200 psi discharge pressure and can tolerate this finer, although still considered “coarse”, level of particulate filtration. To put it in perspective, 100 mesh is equivalent to about 150 microns or 0.006 in. diameter. This may hardly seem coarse when considering the diameter of a human hair is about 100 microns but compared to the generator manufacturer’s engine mounted fuel filters which can be rated as low as 4 or 5 micron, then 150 micron is certainly coarse but worthy of being part of the stages of fuel filtration leading up to the generator engine.
Primary Filters
The final two stages of fuel filtration, primary stage and secondary stage, occur at the generator. These are both part of the generator specification and supplied by the generator manufacturer. Options for both should be evaluated

closely with consideration to selecting the most appropriate options for the application. For instance, if the generator is strictly for standby duty, and the generators are redundant, having redundant filters may not be necessary at the primary and secondary filter locations. However, if the application is prime duty, provisions for changing filters while the engine is in operation should be provided. In this case redundant filters with appropriate valving and pressure gauges are necessary. In some standby installations, the application may not require generator operation for the duration of an extended outage but rather for a short time that provides safe shut down of electrical loads. We’ve found these applications to be rare and more often than not, standby generators are expected to run through an extended outage. In these standby applications, redundant filters should be included.
The bank of primary filters are typically installed adjacent to the generator and may be supported from the floor or generator base frame or both. Primary filters are also commonly called filter/water separators as they provide the last chance to remove water prior to fuel injection. Primary filter rated particle size (micron size) and filter efficiency should be carefully selected in coordination with the generator manufacturer's technical support to provide the best

filtration for the fuel injectors at pressure drops within the engine’s fuel pump suction limitations. In general, maximum 25 micron filtration at this stage is recommended. Primary filters should include rated micron size, efficiency and rated pressure drop labeled directly on the filter housing. A simple vacuum gauge shown at right can be used to indicate when the filter cartridge should be replaced as the vacuum pressure needle approaches the safe limit of the engine fuel pump. The water removal feature of the primary filter should also be carefully chosen. There are two basic types of mechanical water separators available, coelescers and water absorptive filters. Both include a bottom drain valve for collecting and proper disposal of separated water. Coalescing separators are more commonly used and effective at separating water droplets that are suspended from condensation but not as effective at removing water that is emulsified with the oil. Emulsification is defined as a mixture of two liquids that are normally imiscible such as oil and water. Water absorptive filters are more effective at removing emulsified water with today’s fuels. Lubricity additives in today’s low sulphur fuels can have the undesirable effect of acting as a strong emulsifying agent making it more difficult for common coelescers to capture the tiny water droplets. Water absorptive filters are effective at removing both suspended and emulsified water even with today’s fuels and should be considered with primary stage filtration.
Secondary Filters
The final stage of filtration prior to the engine’s fuel injection system is the secondary filter. Unlike primary filtration which is located on the engine fuel pump suction side and includes water separation as well as particle filtration, the secondary filter is located on the pump discharge side and is a low micron particle filter only. Examples below show different applications of secondary filtration on a stationary diesel engine generator. Figure-A shows redundant filtration using dual secondary filters and Figure-B shows a single, non-redundant secondary filter example.

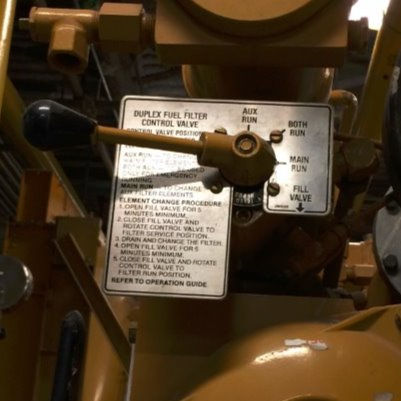
Figure A - Main and Auxiliary Secondary Filters – CAT 3516 Example Stationary Diesel Generator
Figure B - Single Secondary Filter – CAT 3512 Example Stationary Diesel Generator

The critical size particle that contributes to wear in modern diesel engines is 5 to 7 micron size. It is common to see engine manufacturer’s use secondary filters as low as 2 micron. Using filters with the highest efficiency at the required micron rating is a very important consideration at both the primary and secondary filter locations. Filter efficiency and micron rating should be labeled directly on the filter housing. ISO Standard 16889 specifies fuel filter cleanliness performance levels and filter test methods for efficiency ratings known as Beta Ratios. The test method uses multiple filter passes with test dust of a known particle size. The test is concluded and the filter is rated when the pressure drop across the filter element reaches a specified limit or the Beta Ratios fall below a specified level. The test also rates the filter elements ability to maintain its efficiency at the micron rating after the rated pressure drop is exceeded. This is known as the filter elements Beta Stability. The important thing to understand is that filters that are labeled with micron ratings but without labeled efficiencies do not necessarily provide the protection you may think you’re getting. A 2 micron filter for example, without a labeled efficiency to back up that claim, is probably letting much larger particles pass through. Ultimately, the wear and tear on the fuel injection parts will show up at the time of engine preventative maintenance or beforehand in poor performance or injector failure. If attention to providing good fuel filtration is made at all stages between the bulk storage tank to the injectors, the engine will be allowed to perform at its best providing many hours of efficient, reliable operation, protecting it from potential fuel oil contaminants.
Polishers
Fuel polishing systems employ 3 stages of filtration that usually includes a 100 mesh strainer as the coarse, 1st stage filter with a finer stage and a water removal stage that follow. Polishing systems can be very effective and should be included as part of the bulk storage tank system. When properly piped, the polishing system can be an effective way to remove water and sediment that settles to the bottom of the bulk storage tank thus preventing sludge from building up. The polishing system inlet piping should extend down to within 1” to 2” of the tank bottom at the low point end of the tank with the discharge piped similarly but at the opposite end to provide a “sweeping” of the tank bottom. A sufficient polishing unit pump size should be selected to cause turbulence which improves sweeping of the contaminants. Sizing the pump and pipe size is a balance between providing sufficient turnover within reasonable run times. Oversizing of the pump/piping can be avoided by allowing for periodic long run times for the polishing operation that provides sufficient turnover of the tank bottom contents. It is important to keep in mind that the fuel transfer pump inlet piping is required to be approximately 6”above the tank bottom to avoid transferring any water or sediment that may have accumulated at the bottom. This is good practice and helps to keep the foot valve inlet screens from becoming clogged. Even though generators may be frequently exercised and stored fuel turn over rates may be high, the bottom layer of fuel containing water and sediment remains there. Polishing systems that are properly sized and piped as described above can be very effective at mitigating this bottom layer of contaminants. Benefits include prolonged life of fuel filters and avoiding filter plugging before the scheduled service and prolonging the life of the fuel injectors providing efficient and reliable engine generator operation.
Comments